Few challenges across the asset management landscape are as critical—or as complex—as balancing cost and risk. Stock too little, and you risk operational downtime. Stocking too much, results in free cash flow tied up in working capital. Either scenario creates a risk to organization’s profitability. The key to striking the perfect balance? A well-defined part criticality strategy.
This strategy becomes even more powerful when integrated with the MRO Lifecycle, a framework promoted by Xtivity to complement the ISO 55000-defined Asset Management Lifecycle. Organizations can optimize inventory decisions and achieve their business objectives by aligning part criticality with the three stages of the MRO Lifecycle—Part Introduction, Active Use, and End of Use.
This article will explore how part criticality fits within the MRO Lifecycle and how decision-support tools can simplify the complexities of managing large datasets and dependencies.
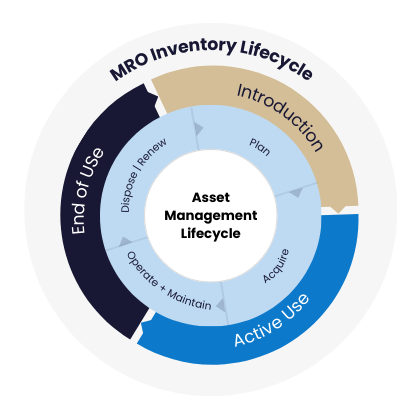
What Is the MRO Lifecycle?
The MRO Lifecycle is a strategic approach to managing Maintenance, Repair, and Operations (MRO) inventory in harmony with an asset’s lifecycle. Its three stages—Part Introduction, Active Use, and End of Use—help organizations plan and manage inventory requirements across the entire lifecycle of their assets.
At each stage, asking the right questions and leveraging decision-support tools ensures that inventory strategies align with business objectives, reduce risk, and optimize costs.
Stage 1: Part Introduction
This stage focuses on integrating new parts into your inventory system as assets are commissioned and maintenance activities are planned. It is the perfect time to establish part criticality and align stocking decisions with operational needs.
Key considerations during Part Introduction include:
- Auditing existing inventory: Ensure no redundancy with parts already in stock.
- Evaluating operational impact: Identify parts that are mission-critical for maintaining uptime.
- Forecasting demand: Use historical data to predict future usage and avoid overstocking.
- Assessing supply options: Identify dependable suppliers with competitive pricing and manageable lead times.
The goal in this phase is to ensure that new parts are carefully evaluated, prioritized, and introduced into your inventory system while minimizing the risk of excess inventory or critical shortages. Decision-support tools can help analyze data at this stage, uncovering gaps and opportunities for optimization.
Benefit Highlight: Obsolescence avoidance starts here. A structured approach ensures only necessary items are added, minimizing long-term costs.
Stage 2: Active Use
During the Active Use phase, inventory management shifts toward ensuring part availability while balancing costs. This is when parts are consumed regularly to support ongoing operations, and stock levels must adapt to changing demands.
Key strategies include:
- Analyzing consumption patterns: Use historical data to forecast demand and adjust stock levels proactively.
- Automating replenishment: Streamline ordering processes to maintain availability without overstocking.
- Implementing criticality-based stocking: Prioritize essential parts to minimize downtime.
- Maintaining supplier relationships: Ensure consistent part availability by collaborating closely with your suppliers.
Benefit Highlight: In this Phase, leverage real-time analytics to strike the perfect inventory balance. Avoid stockouts, cut excess, and keep operations flowing—all while reducing costs and boosting supply chain efficiency.
Stage 3: End of Use
As assets near the end of their lifecycle, the End of Use phase becomes crucial for minimizing waste and mitigating obsolescence risks. Inventory strategies must shift from replenishment to thoughtful reduction.
Key steps include:
- Mitigating obsolescence risk: Identify parts nearing obsolescence and phase them out gradually.
- Managing inventory run-down: Align inventory reduction efforts with equipment decommissioning timelines.
- Exploring alternative uses for parts: Repurpose or reallocate surplus parts to other projects or facilities.
Benefit Highlight: This phase emphasizes resourcefulness. By carefully planning the decommissioning process, organizations can minimize excess inventory, recover value from unused parts, and contribute to sustainability
Why Part Criticality Matters Across the MRO Lifecycle
A part criticality strategy is not just about ranking parts by importance; it is about asking the right questions and aligning inventory decisions with business objectives at every stage of the MRO Lifecycle.
Here’s how part criticality enhances the MRO Lifecycle:
- In Part Introduction, it helps prioritize essential items, reducing redundancy and optimizing stocking decisions.
- In Active Use, it ensures that critical parts are always available without inflating inventory costs.
- In End of Use, it identifies opportunities to phase out obsolete items while recovering value from surplus inventory.
By applying part criticality within the MRO Lifecycle, organizations can make smarter decisions, avoid costly mistakes, and achieve greater operational efficiency.
The Role of Decision-Support Tools
Managing the complexities of the MRO Lifecycle often requires handling vast datasets and interdependencies. This is where decision-support tools such as Xtivity’s Pulse IO come into play.
These tools can:
- Analyze historical data to predict demand and optimize stocking decisions.
- Highlight critical dependencies between parts and assets.
- Provide actionable insights to mitigate risks, such as stockouts or excess inventory buildup.
By leveraging these tools, organizations can make data-driven decisions that support their inventory optimization goals while staying aligned with the Asset Management Lifecycle.
Bringing It All Together
Mastering part criticality is a journey that spans the entire MRO Lifecycle. From introducing new parts to managing their active use and planning for their end of life, every decision has a ripple effect on cost, risk, and operational performance.
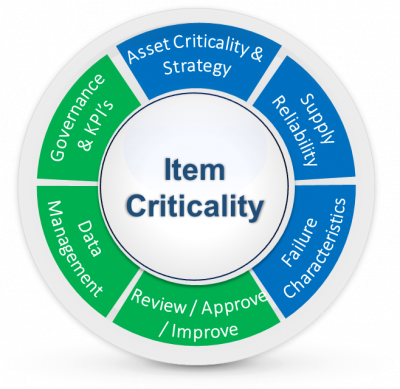
Key Benefits Provided by Parts Criticality
- De-Risk Operations – Ability to identify and mitigate potential production, environmental and safety impacts associated with failing parts / components.
- Effective Asset Management – Identification of critical parts and components that impact an asset’s ability to perform as required.
- Operating Profit – Mitigating unplanned equipment downtime, costs associated with breakdown maintenance, and non-moving part provisions / write-downs.
- Better Working Capital Allocation – Criticality-based stocking decisions driving focus on parts that matter most, providing opportunities for stock reduction and limiting future stock additions.
Are you ready to take the next step in aligning your inventory strategy with the MRO Lifecycle? Let’s connect and discuss how to balance cost and risk in your operations.
Set up a discovery call to explore Xtivity’s solutions and overcome your unique challenges.