Master Data Management Solutions
Today’s manufacturing companies rely on a complex ecosystem of interconnected software, including Enterprise Resource Planning (ERP) software, to drive business processes and enable quality decisions through accurate insights. These systems all rely on quality data to be effective.
Whether you are looking to raise a Purchase Requisition or issue a part to a Work Order, the quality of your master data makes the difference in the efficiency of your transactions and accuracy of decisions.
With the right master data management tools and data governance in place, including data cleansing tools, descriptive taxonomies and visualization tools, Xtivity will help you improve and maintain the quality of your data.
What this means to your MRO supply chain is that you can run your operations with a focus on improving asset reliability, increasing service levels, right sizing MRO inventory, and improving capital allocation – with confidence that your transactional processes are underpinned by quality information.
What is the Purpose of Master Data Management?
Enterprise Resource Planning Systems (ERP) like SAP, IBM Maximo, JDE, Microsoft Dynamics, Oracle and others lie at the heart of today’s successful companies.
ERPs are driven off a series of data tables linked by transactional workflow and computation engines. These tables are linked by key fields, enabling complex transactions to flow through a series of functional tables.
Those key fields represent your “master data”. And without defined data descriptions, and clear processes for changing these fields, that master data becomes corrupt over time.
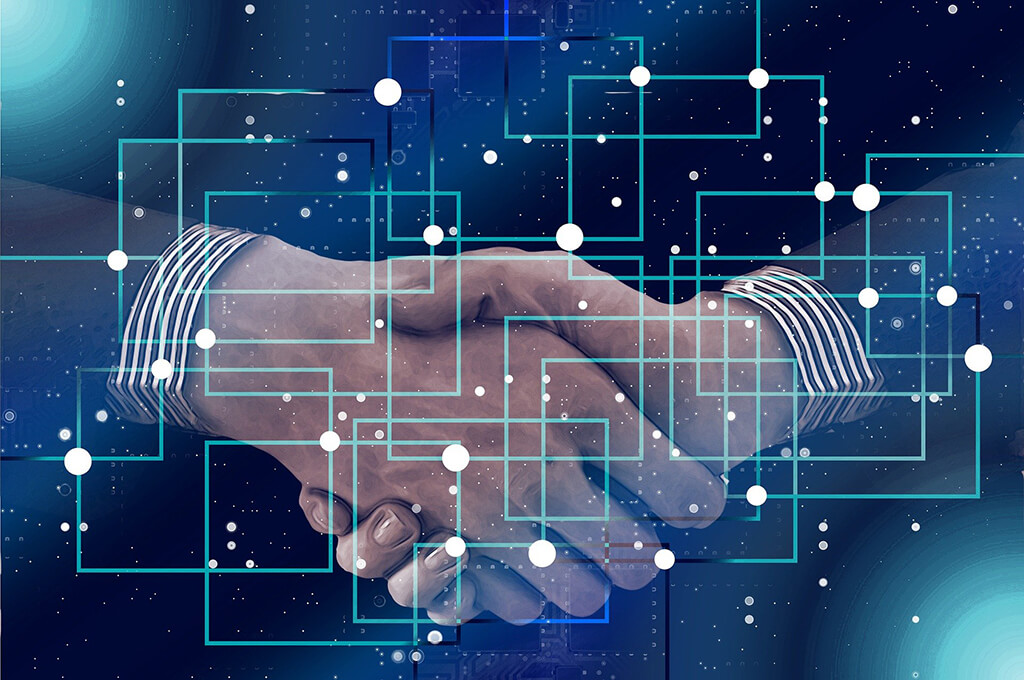
How does this happen?
In a simple example, a part can be defined in the system by three different people, each using a different description and different stocking locations. Now - imagine this duplication occurs across an average parts catalogue of 30,000+ SKUs - and the problem becomes exponential.
Master data management (MDM) helps avoid such issues by defining clear and consistent naming conventions, aligning data attributes, and eliminating duplications. This drives smoother transactional processes including when that data runs through your MRO management software.
Cleansing and aligning data, however, is not enough. Without the appropriate governance policies, procedures, and guidelines also in place, clean data will typically last no more than two years.
That is why a strong master data management program must include data governance principles and processes.
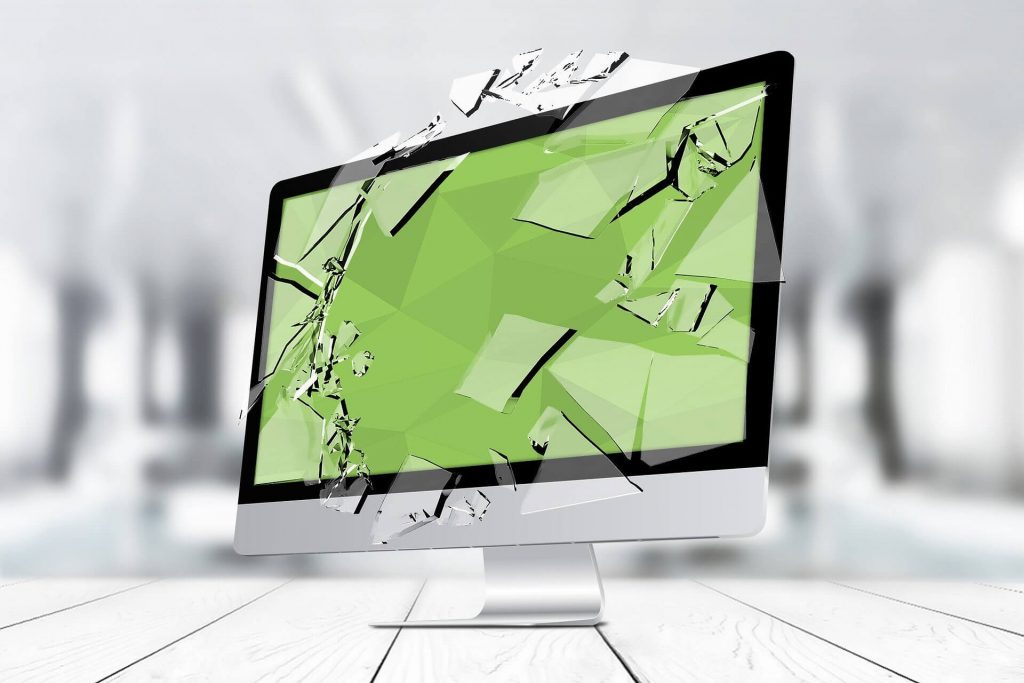
Master Data Management Challenges
Due to “toxic data” in your systems, parts catalogues often contain items with partial descriptions, inconsistent naming taxonomy (noun, modifier, attributes), duplicates with different names and a host of other issues. This creates knock-on problems across departments, from Maintenance Planning to Procurement and Finance.
- How many duplicate parts are you holding in your catalogue with different names, prices, manufacturers and quantities?
- What are duplicates costing you in terms of free cash flow and excess warehouse space?
- How do you know you are purchasing the right parts, in the right quantities, from the right suppliers, at the right price?
- What is the downstream impact on asset reliability, service levels and uptime, if your maintenance department can’t fulfill work orders?
- Are you maximizing pricing for your parts across suppliers?
- How much time does procurement spend chasing updated part and vendor information in order to place a purchase order?
- How many parts bypass the new parts introduction process and are ordered as direct charge, with variable part names?
- What impact is toxic data having on your aging and obsolete inventory, as it drains your working capital?
Master Data Management Solutions: How Xtivity Can Help
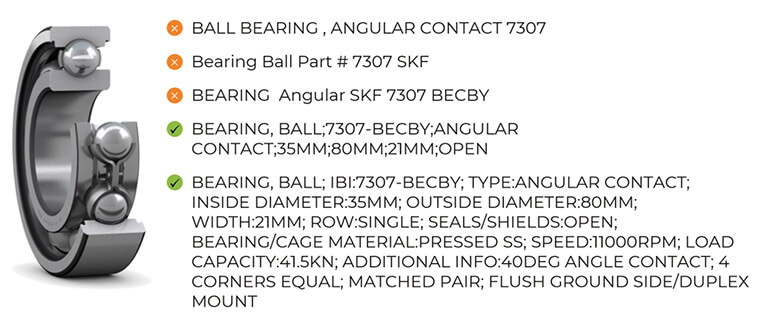
Xtivity provides solutions and services to help organize, structure, cleanse and enrich your parts data. And we further help develop a master data governance process to ensure a high level of parts data quality ongoing.
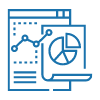
Data Analysis
We typically begin by identifying the current state of your data integrity. We identify what opportunities exist, and where to focus to generate the most impact on improving your master data quality.
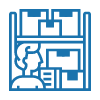
Parts Ordering Alignment
Through Xtivity’s MRO Inventory Optimization Solution, we help you establish baseline ordering value (min/max / lead time) recommendations for each cleansed item. This provides accurate current-state for integration with your ERP. And, if you choose to continue working with Xtivity’s MRO Inventory Optimization Solution, we provide you the MRO Optimization Software and assistance to ensure you are always maintaining the right inventory against your cleansed data.
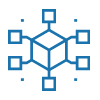
Data Structuring and Data Cleansing
You may already have a corporate data taxonomy in place that we can leverage; or require Xtivity’s help to develop that data structure. Either way, we use that data structure as the baseline to conduct a data cleansing process and transform inaccurate and inconsistent data into consistent quality data.
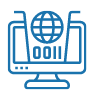
Parts Enrichment
Xtivity can help you enrich select data through various mechanisms, including contacting your vendors to add rich parts information.
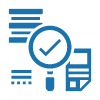
Data Governance
Finally, to ensure ongoing high quality data integrity, Xtivity helps clients develop the processes, procedures and structures to drive ongoing success.
What are the Benefits of Improved Master Data Management?
When combined with an MRO Inventory Management Solution, a robust Master Data Management Solution generates benefits for multiple stakeholders.
Maintenance & Reliability
- Increase wrench time
- Support comprehensive Equipment Maintenance Plans (EMPs)
- Ensure complete asset Bill of Material (BOMs)
- Identify critical spares
Procurement
- Reduce excessive Purchase Order administration costs and rework
- Leverage spending though volume-based discounting and holistic supplier strategies
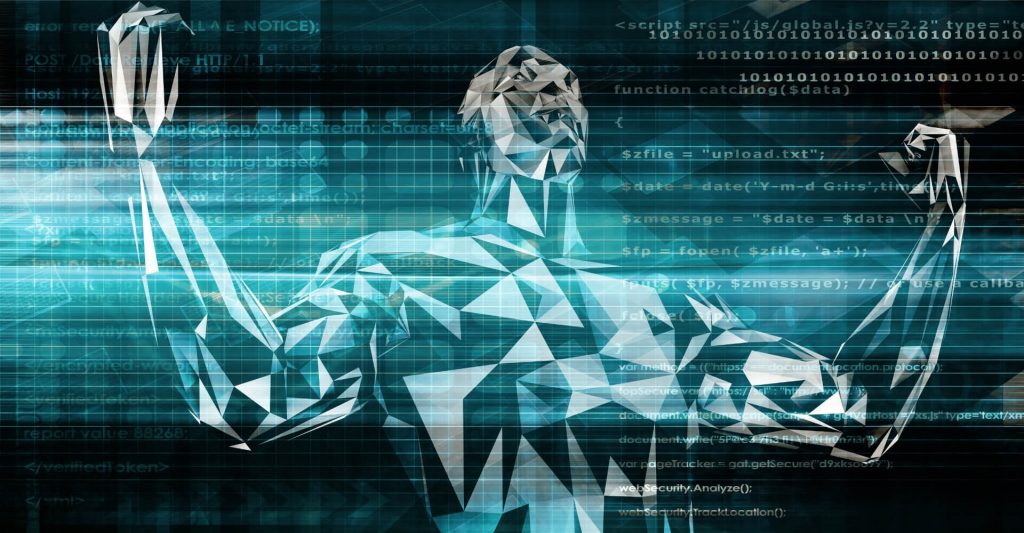
Warehouse & Inventory Management
- Ensure that the correct parts are ordered, in the right quantities, with reliable lead times. And reduce stock outs
- Reduce material handling costs
- Minimize duplicate inventory stocking
- Increase your turn rates
- Better manage warehouse space constraints
Operations
- Ensure asset uptime and high equipment service levels
- Increase productivity and throughput
Finance
- Maximize your Working Capital allocation
- Reduce your excess MRO inventory carrying costs
- Reduce Accounts Payable administration by reducing discrepancy resolution time