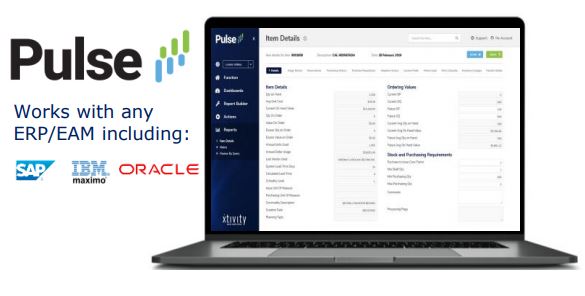
A well-designed inventory management program should be focused on improving inventory mix and ensuring you have what you need to support ongoing operations. But allocating finite working capital to ensure the right part is in the right place at the right time is always a challenge.
This is where an effective parts inventory optimization system comes into play. And the baseline for a robust solution is provided through Xtivity’s MRO Inventory Optimization Solution.