Obsolescence Management
What is it?
Inventory can be made obsolete due to a number of factors, these can include:
- ● Part specification change
- ● Asset upgrades
- ● Decommissioning of supported Assets & Equipment
- ● Material degradation
Regardless of the reason, if left unaddressed, this inventory segment represents a drain on administrative, physical and working capital resources. Obsolescence is a fact of life. As soon as a part is put into inventory some degree of obsolescence risk is accepted – but this does not mean the risk should be unmanaged.
Pressures to do “more with less” applies to inventory management as other areas of your business. Maintaining the appropriate mix of inventory to support ongoing operations is critical. Working Capital and space are generally in short supply. This environment does not allow the luxury of holding onto stock, that is not and will never be issued from stores.
So why would we hold inventory that no longer supports our business? The answer is dealing with obsolescence can be complex, time consuming and highly subjective. While its generally agreed that addressing obsolete inventory in a timely manner is leading practice, few organizations have the time, resources or desire to make this part of their monthly operating rhythm.
We start by reviewing the governing policies. Some companies have a strong set of rules regarding how inventory should be classified, others do not. Without clear policies in place, it is near impossible to gain alignment on the decisions that follow.
The next step is data analysis. Here we use our proprietary tools and techniques to profile your inventory, identifying where to direct limited resources to assess stock and determine if it is active or obsolete.
Once completed, we will work with the client team to walk down and assess stock, ensuring that if it is to remain in inventory, it is ready to support operations.
Finally, we will facilitate cross functional working sessions to align on decisions and action plans aimed at dispositioning obsolete inventory and agreeing on the processes going forward to ensure operational relevancy is maintained.
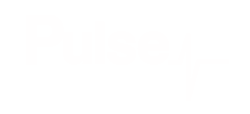